アルマイトとは?
アルマイトとは、アルミニウムを陽極で電解処理することによって、人工的に酸化皮膜を生成させる処理を言います。
陽極酸化処理が正式な表現で「アルマイト」は「アルミニウムの陽極酸化皮膜」の総称です。
一般的にアルマイト処理と呼ばれるものには、封孔品とよばれるもの、複合皮膜(電着塗装)と呼ばれるものや、硬質皮膜などがあります。
(それぞれJIS H 8601、JIS H 8602,JIS H8603と区別されています。)
その他にも二次電解着色法や染色法、アルマイトを利用した塗装処理なども施され、色彩豊かな表現が可能です。
最近では、各種表面処理方法等の組み合わせを工夫することよって、アルマイトの多様化・高級品化・個性化等の試みが多くなってきています。
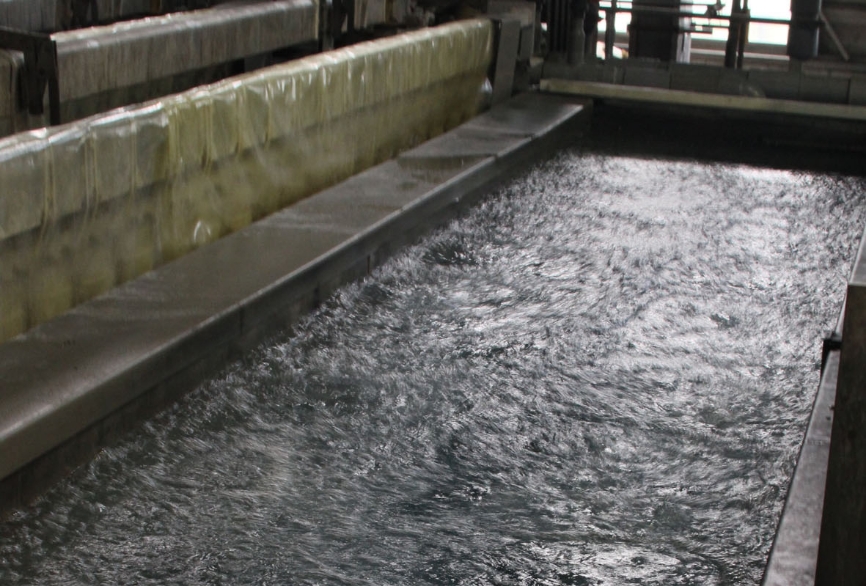
なぜアルミニウムに表面処理が必要か?
アルミニウムの表面は、自然酸化皮膜で保護されているので一般に耐食性がよいといわれています。
しかし、この皮膜は非常に薄いので、あらゆる環境に耐えることはできません。
アルミニウムそのままでは、下記のようなデメリットがあります。
・水分や汚染物質、異種金属との接触により腐食する。
・柔らかい金属の為、傷が付きやすい。
・色調が単調で変色しやすい。
これらを防ぐ手段として、表面処理が必要になります。
アルマイトのメリット・デメリット
アルマイト処理を施すメリットとデメリットを、下記にまとめました。
- メリット
- ・硬度・耐摩耗が上がる
・表面の変色や腐食を防止できる
・様々な色彩が得られる。
・耐用年数が得られる。
- デメリット
- ・生地での使用よりコストが掛かる
・使用環境に応じた仕様選定が必要(知識が必要)
・色彩のコントロール(微調整)が難しい
・材料起因の不具合が出る
アルマイト皮膜は非常に硬く、アルミニウムそのものに比べ熱によって伸びません。
その為、高温にする、曲げる等の応力が加わることでクラック(皮膜割れ)が発生しやすくなります。
使用用途に応じた、適切な表面処理が必要になりますので、我々表面処理のプロが必要です。
アルマイトの化学反応│陽極酸化とは?
陽極酸化処理とは、一般的にアルマイト処理とも呼ばれています。
アルミニウムを陽極とした電気化学的方法を用いて、人工的に酸化皮膜を生成させる処理です。
アルミニウムを陽極として硫酸電解液の中で電気分解をすると、下記のような反応が起こります。
陽極反応 | 陰極反応 |
---|---|
Al → Al3+ + 3e– OH– → O2- + H+ HSO4– → SO42- + H+ |
H+ + e– → H2 ↑ |
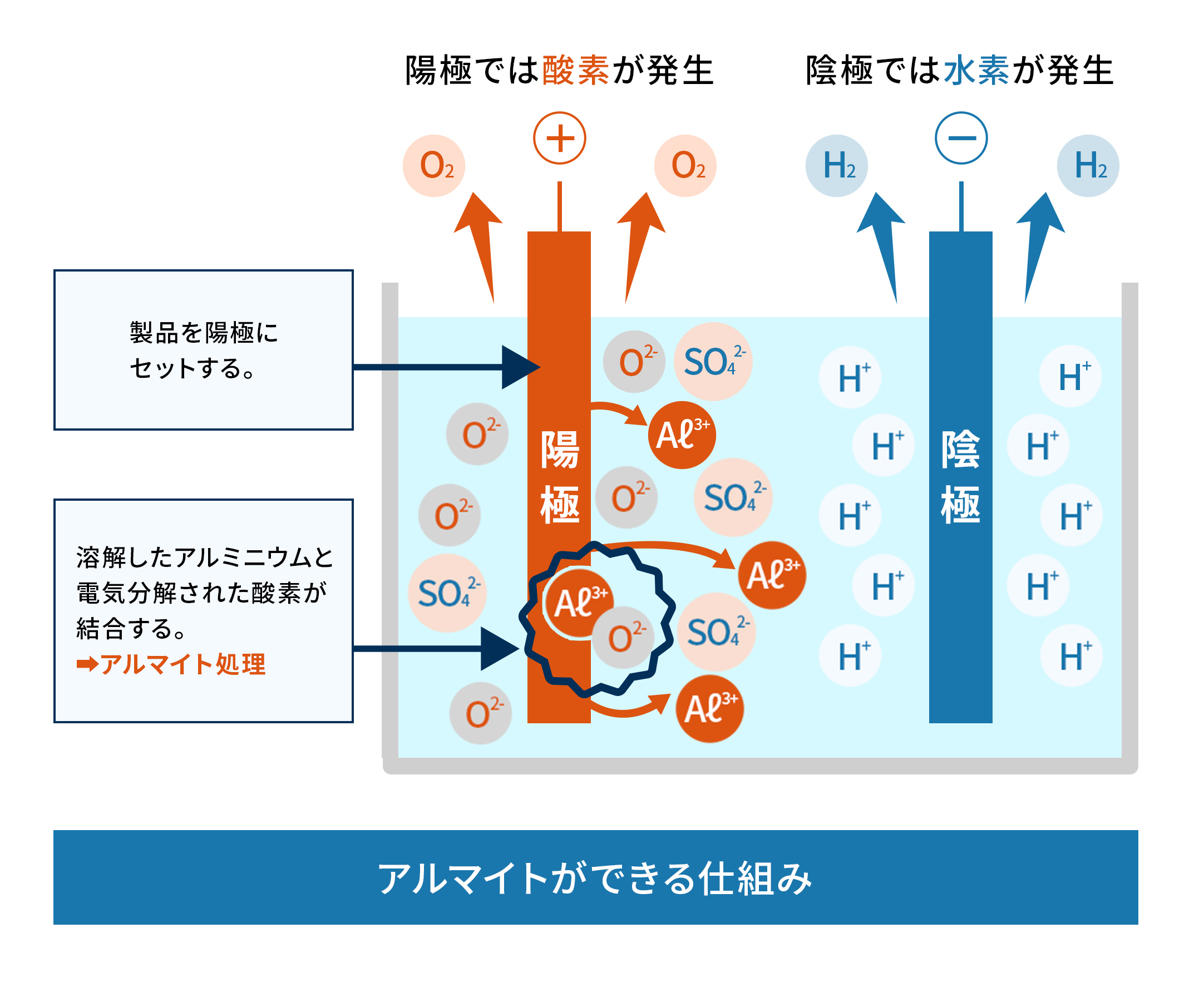
上記のように、硫酸根を含む酸化皮膜の生成が進むのです。
この反応が進んでいる間、アルミニウムの表面でどのような変化が起こっているのかより詳細に図に表すと、次のようになります。

なお、アルミニウムの性質は、合金化することにより、かなり変化します。
下記の表に、純アルミニウムの一般的性質をまとめてみました。
純アルミニウムの物理的・化学的性質一覧表
項目 | 特性 |
---|---|
原子量 | 26.9 |
原子番号 | 13 |
結晶構造 | 面心立方 |
格子定数 | 4.0496×10-8 cm |
密度 | 2.70 g/cm3 |
線膨張係数 | 23.7×10-6 /K |
融点 | 660.4 ℃ |
融解熱 | 10.7 KJ/mol |
沸点 | 2470 ℃ |
蒸発熱 | 291 KJ/mol |
比熱 | 24.3 J/(K・mol) |
熱伝導率 | 237 W/(m・K) |
電気伝導率 | 37.66 S/mm2 |
比抵抗 | 0.02655 Ω・mm2/m |
抵抗の温度係数 | 4.2×10-3 |
電気化学当量 | 0.3354 g/(A・h) |
磁化率 | 0.61×10-6 cm3/g |
ヤング率 | 68.3×109 N/m2 |
剛性率 | 25.5×109 N/m2 |
ポアソン比 | 0.34 |
アルマイトとメッキの違い
金属を被覆するという意味で、アルマイト(陽極酸化処理)とメッキが同じだと思われていることも少なくありません。
しかし、アルマイトとメッキは全く異なる表面処理方法です。
2つの違いを、下記の図にまとめました。
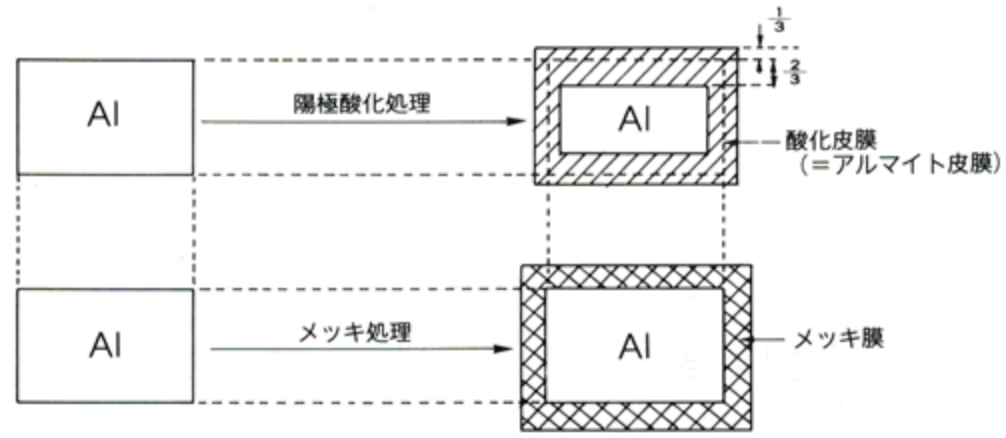
メッキは陽極で電解を行うアルマイトとは異なり、陰極で電解を行い、電解液の金属イオンを還元析出して表面処理を施します。
被加工材の上に異種金属の膜が重なるため、重ねた膜の分だけ、元の金属より厚くなる点が特徴です。
一方アルマイトは、陽極でアルミニウムを溶かし、その溶かされたアルミニウムが「Al2O3」という酸化物に変化して酸化皮膜ができます。
そのため、皮膜が内部に進行し、アルミ表面に沿って皮膜処理が行われるのです。
RECRUIT
採用情報
CONTACT
お問い合わせ
GROUP
グループ企業